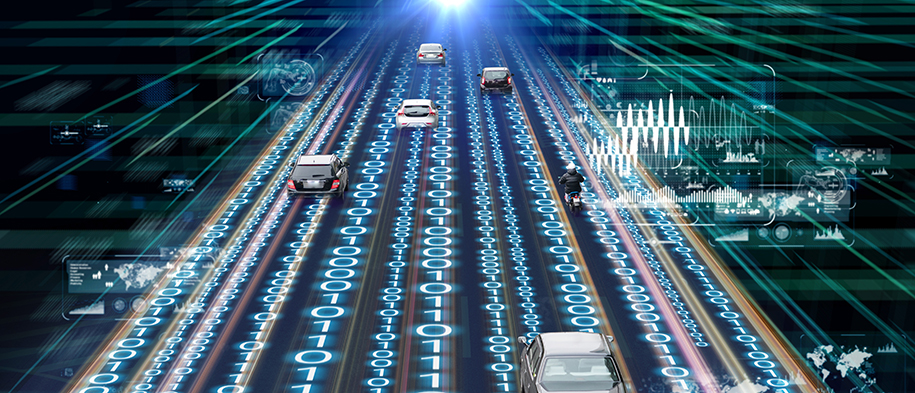
“There’s a way to do it better - find it.”
Thomas Edison
Connect Plus
Research and development
Innovation is a fundamental principal of our contract.
We are continually exploring new and innovative ways to deliver safer, more reliable journeys for our customers while at the same time limiting disruption and providing a safer environment for our workforce.
To this end there is a continual drive to investigate developments in asset management techniques and technologies, either looking at already available or emerging technologies both in the UK and from across the world.
Additional benefits will include the effective management of the project lifecycle and reduction of the whole life carbon and cost impacts.
How we manage innovation on the M25 is critical, that is why we all work collaboratively to ensure it is embraced and embedded within our culture, giving rise to improvements in our delivery and productivity.
We manage innovation through a standardised and systemised approach, this is our innovation process, detailed below. This process ensures any ideas that are put forward follow the same consistent approach across the whole community.
We openly encourage and support innovation with our framework contractors and our wider supply chain partners. Our Innovation Steering Group continues to drive our innovation strategy across the project, working towards a vision of creating and maintaining a sustainable and supportive innovative community culture, by putting in place a strong and effective innovation programme.
Our aim is to make innovation a part of everything we do, from the products we use to the systems and processes we employ across the organisation. It is by being open to new ideas and solutions, and innovative longer-lasting materials that we will deliver value to our customers, our community, National Highways and the wider industry.
There are three main groups involved in managing innovation on the M25: The Innovation Board, The Innovation Steering Group and the Innovation Working Group.
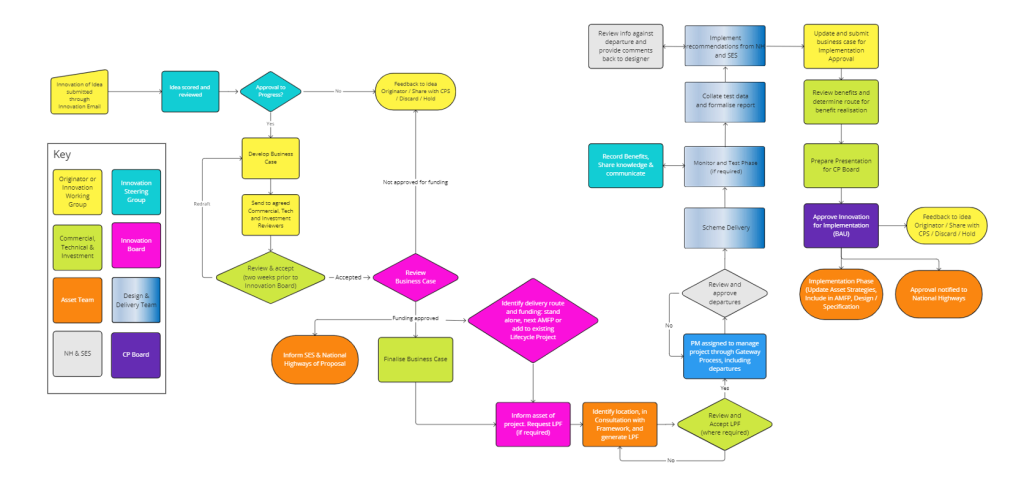
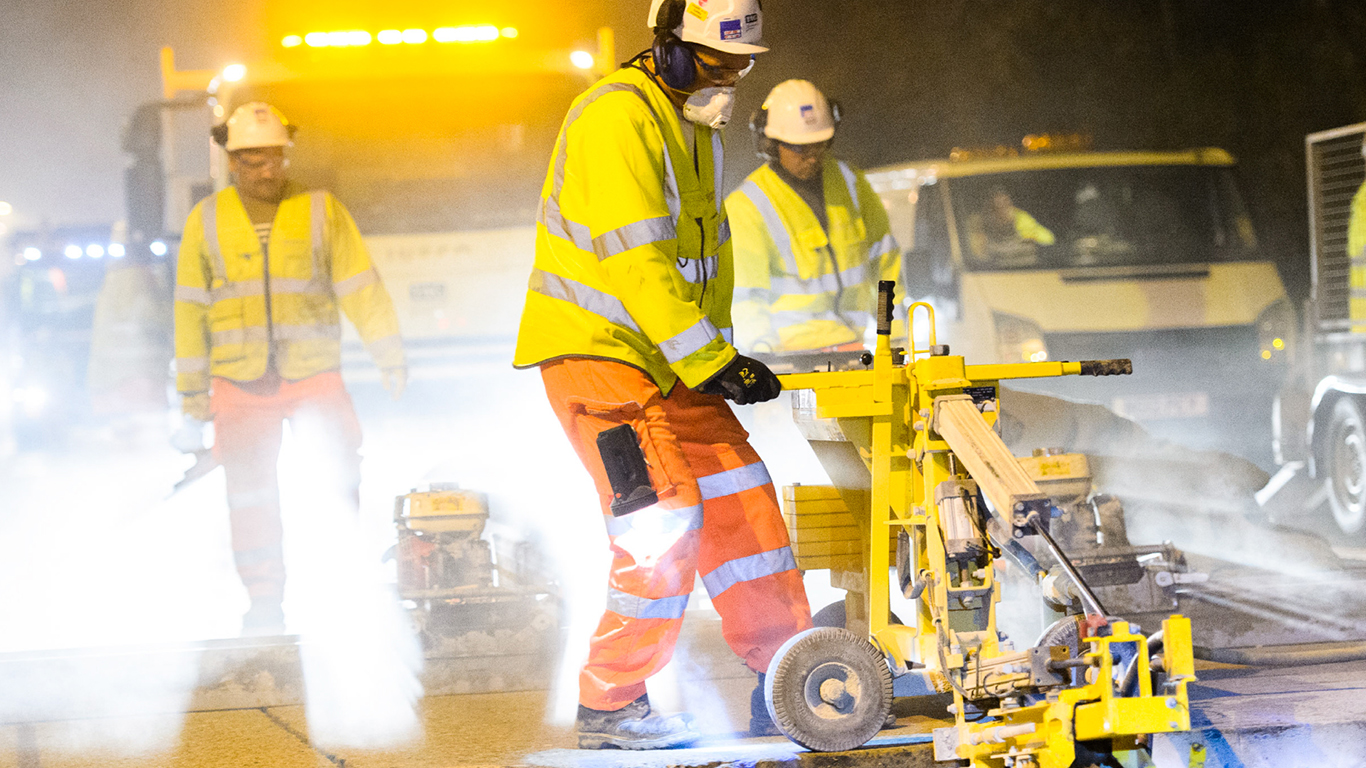
This system, developed by MATtest, is a combination of technologies which improve the testing of asphalt during the construction process. Traditional testing is usually carried out by a technician onsite which can present safety hazards as well as missed opportunities to gather valuable information about the road surface.
The data is processed in real time which ensures that the operatives deliver the work right first time. It is also stored in a useful format which will ultimately add value to the asset management process, beyond just quality assurance. Trials have been completed in Year 10 and a Departure from Standard has been secured for use on the M25 Network in Year 11.
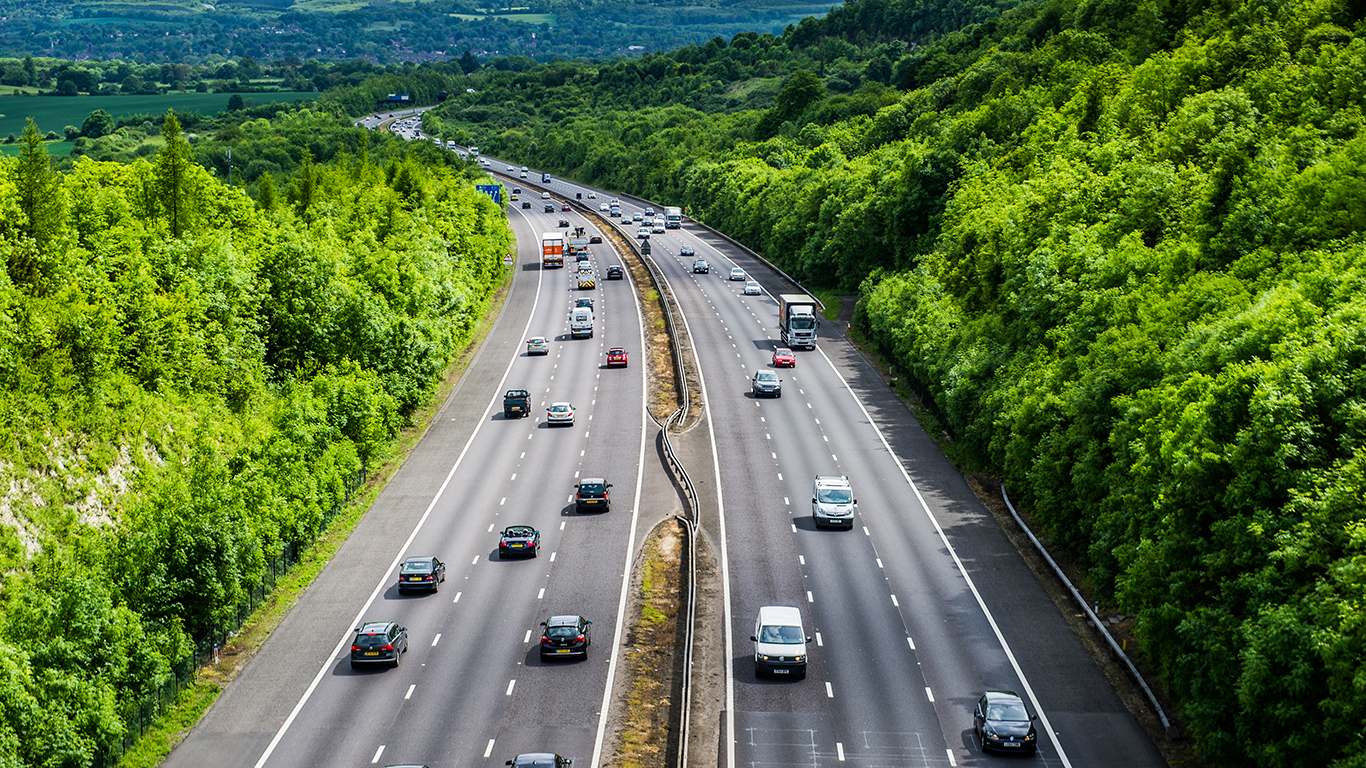
Concrete, in the long term, is a more durable and therefore economically viable road construction material. That’s why, to achieve challenging Department for Transport targets to improve its surface quality, we’re trialling different concrete surface treatments on a stretch of the M1.
The trials started in September 2018 and, using an extensive testing and monitoring regime, will continue for the next four years. Before starting the physical trials, we researched pioneering technologies from around the world, using the findings to inform our decisions. As a result, in one of the trial sections, we’re using a longitudinal grinding machine that we brought in especially from the USA. Our research showed that it’s being used in America with great success on high speed motorways and at airports.
Our initial results have been encouraging and we’re thrilled that some of our customers have picked up on the work we’re doing. There’s still a long way to go as we continue to monitor each treatment against a range of attributes. We’re confident that, even at this early stage, we’ll find a solution that will not only have an immediate impact on the road surface, but will also show long-term benefits for years to come.
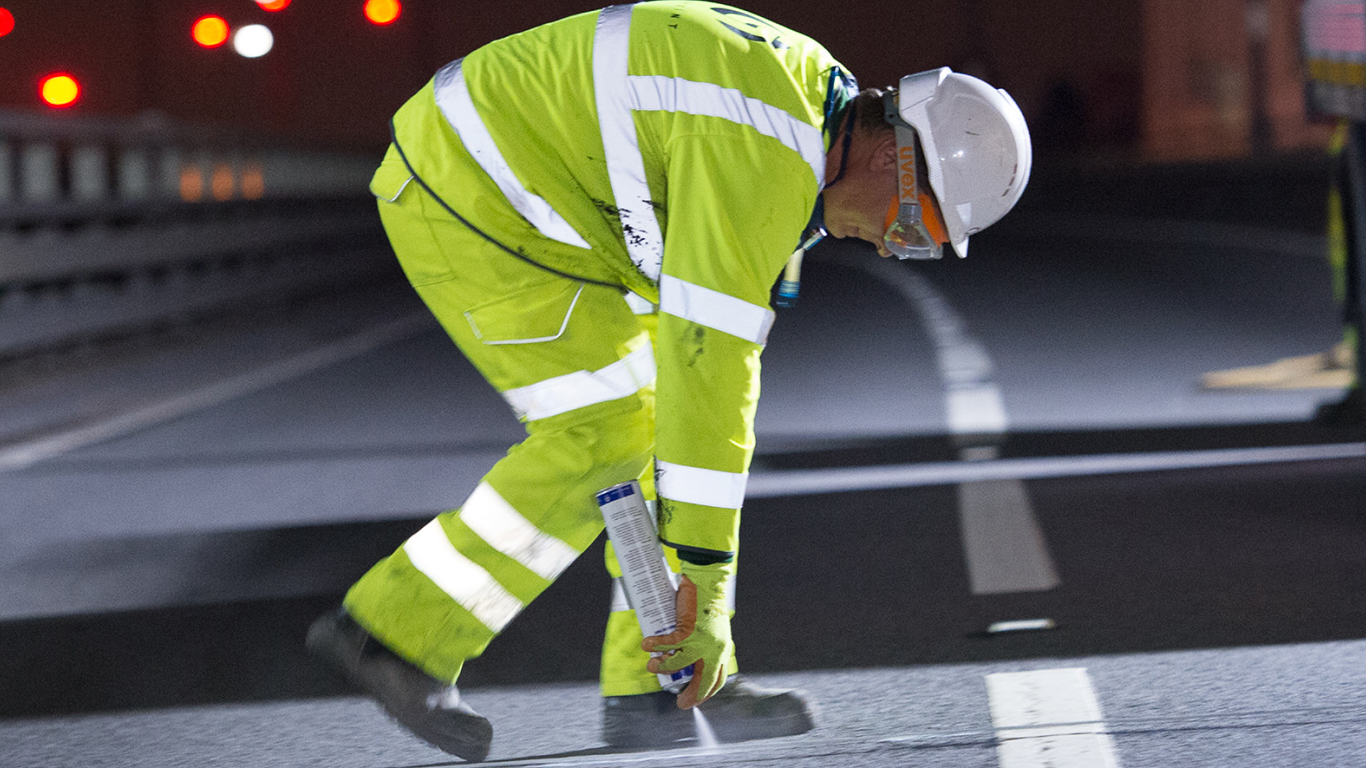
Year 10 saw the second year of installing radar detection in lieu of induction loops removed as part of the pavement renewal programme. Using radar removes the need to install full width pavement patches in preparation for induction loops which often requires additional shifts. It also reduces the number of transverse pavement joints, eliminates the risk of potholes forming around the loops and reduces the risk of MIDAS faults. 26 were installed this year, an increase from 18 in Year 9. Additional improvements in Year 10 included further TM sharing and a reduction from two to one detection heads.
Connect Plus
Research and development